Get a FREE ebook with your print copy when you select the "bundle" option. T&Cs apply.
- Shop
- KoganPage+
- Discover
- Resources For...
- Authors
- About
- Shop
- KoganPage+
- Discover
- Resources For...
- Authors
- About
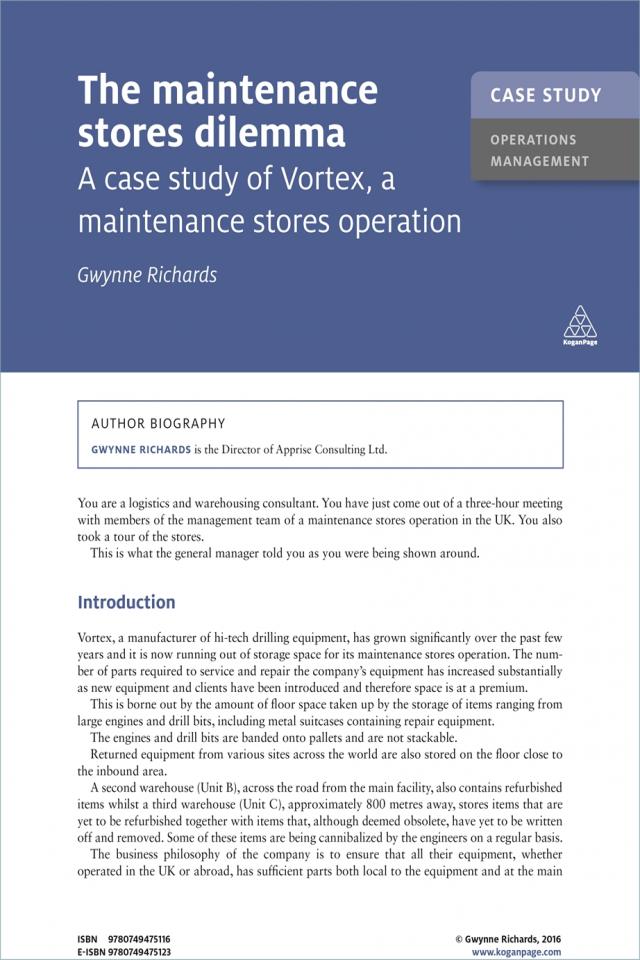
Case Study: The Maintenance Stores Dilemma
A Case Study of Vortex, a Maintenance Stores Operation
FREE UK and US delivery
Bulk buying for your team?
Contact us for exclusive discounts!
About the book
The Maintenance Stores Dilemma explores warehouse operations at Vortex, a manufacturer of hi-tech drilling equipment running out of storage space for its maintenance stores operation. Aimed at students on warehouse management courses, it looks at issues such as increasing requirements for new equipment, shortage of space and the resulting delays to services to clients. It assesses solutions such as proper warehouse planning and the redesign of space in order to improve logistics performance.
The author presents a wide variety of problems and the suggested solutions. The Maintenance Stores Dilemma helps readers put together a sustainable and flexible warehouse operations plan. Gwynne Richards illustrates problems that can arise when managing a warehouse, based on his own experiences of working with a number of clients over the years.
Register for a Kogan Page account at check-out to access and download your PDF after purchasing. You'll also have an opportunity to sign up when receiving your purchase confirmation email.
About the authors
Bulk buying for your team?
Contact us for exclusive discounts!
FREE UK and US delivery
Shipping and handling
Cancellations and returns policy
FREE UK and US delivery (more info)
Kogan Page GPSR
Bulk buying? Contact us for exclusive discounts!
Get exclusive insights and offers
EU Representative (GPSR)
Authorised Rep Compliance Ltd
Ground Floor, 71 Baggot Street Lower, Dublin, D02 P593, Ireland
www.arccompliance.com
Kogan Page GPSR
View the series
Related products
Related content
Subscribe for inspiring insights, exclusive previews and special offers
Headless Content Management with Blaze